Using vision for food depositors
Sometimes you need some help to produce the best products you can. Especially in the food industry, as they are often not completely standardised. Or it is hard to control the position on the conveyor during the production process.
Valuable new functionalities
Fortunately, some solutions can make your life a lot easier. One of these solutions is the use of vision systems. FoodJet has integrated this technology as a helping hand. As a result, various previously impossible, yet valuable functionalities can be added to your depositing process.
Reasons for using vision
We use vision technology for several reasons:
- Position detection
- Shape detection
- Quality control
- Rotation detection
- Statistics
Let's get in touch and discover the possibilities for your production.
Detecting the position of products
If you simplify things, there are two main solutions which are able to detect the position of products:
- Using photoelectric detection sensors - this works very well if products are well aligned across the conveyor. It is simple to program and does not require a lot of knowledge to modify if necessary. In most cases, you do need a sensor for each lane of product. The sensor fails if products are misaligned. The material will be applied off-center, resulting in rejected products and dirty conveyors.
- Vision systems - in case products are misaligned, or you want to collect valuable information on the products you are producing, a camera scanner is the right option
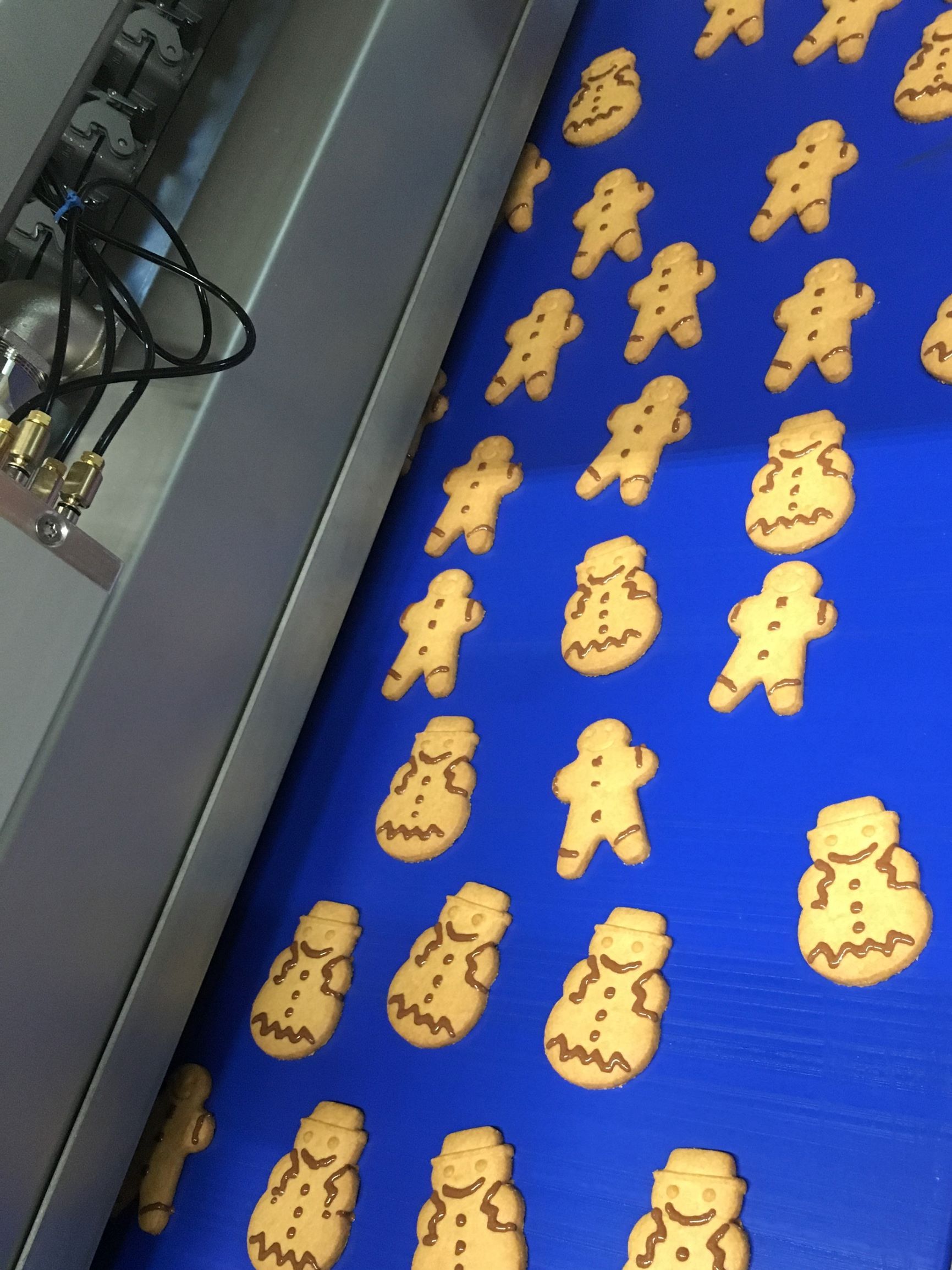
Shape detection
Often products do not have a uniform shape or size. They can be too long or too short, too big or too small, or perhaps deformed somewhere along the process. The FoodJet technology is able to recognise these rejects and will refrain from depositing material on them. This makes it easier for operators to find and remove these products.
Shape detection can also serve a different purpose. When you are running more than one type of product on your line ( for example, a rotary with four different cookie shapes ), the vision system can distinguish between the different shapes and individually select the deposit pattern, based on the identified shape.
Quality control
It is possible to make the FoodJet depositor part of your quality control. You can set parameters for your products. If products are out of specification, alarms can be set to warn the nearest operator. This makes it easier to remove products before they hurt your downstream operations like packaging.
Rotation detection
Some products cannot be aligned because of their shape. Yet you still want to apply a material to increase the value or you simply want to create a new product all together. The FoodJet vision system locates products on the conveyor, even if they are not aligned. Next, it can determines the rotation of the products. This makes it possible to apply all kinds of patterns or designs even if products are not facing the same direction.
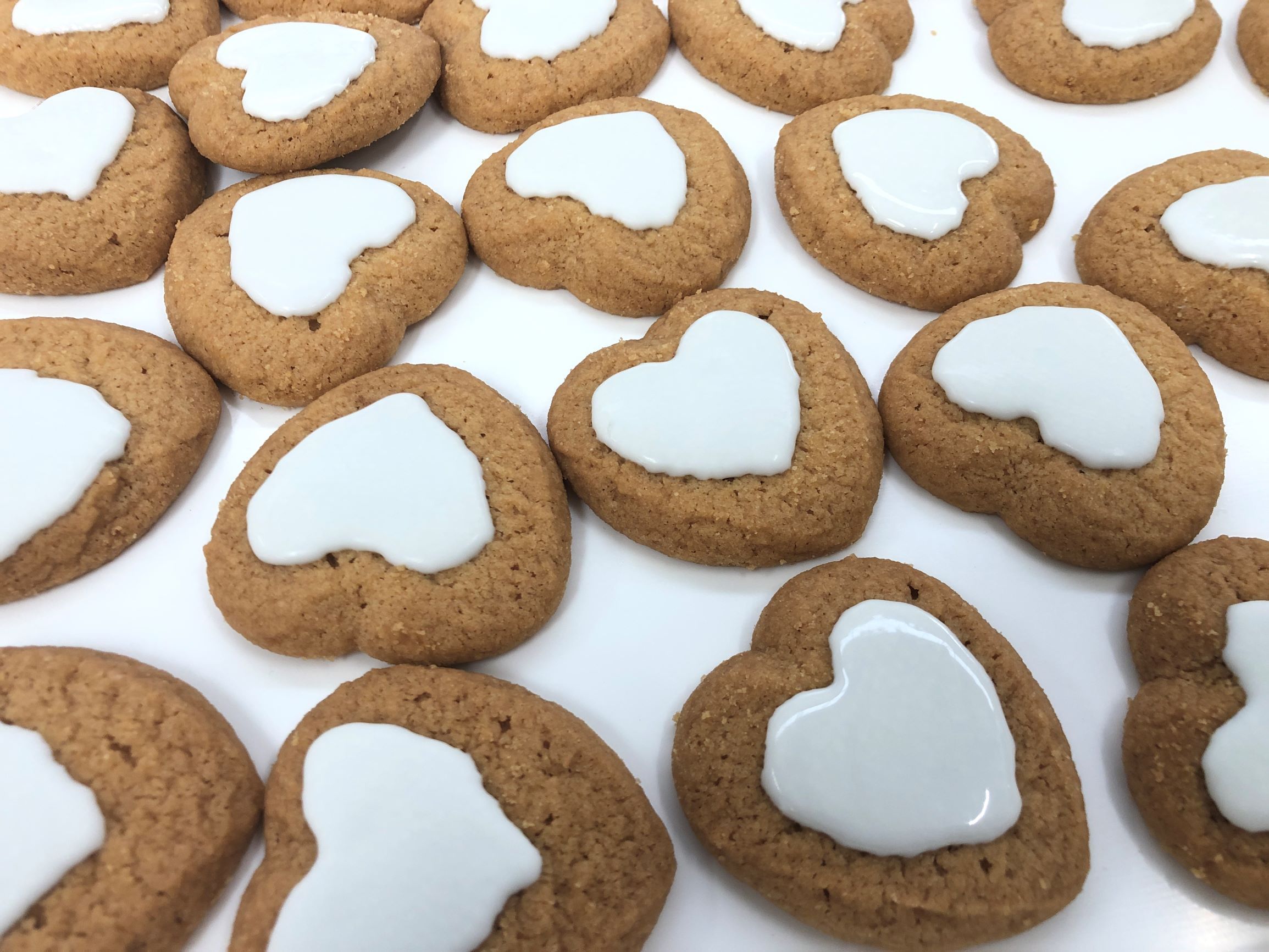
Statistics
With the Foodjet vision system you can collect all kinds of information that will make your production process more efficiently:
- Number of products produced
- Number of products within specification
- Quantity of material applied
- And much more...
All data can be presented on screen and saved for later retrieval.
Unique depositing technology
The FoodJet depositing technology offers the flexibility that makes it possible to optimally use the power of vision systems. The array of nozzles in each depositing head can follow products regardless of their position on a conveyor. No other food depositor makes for such a good match.
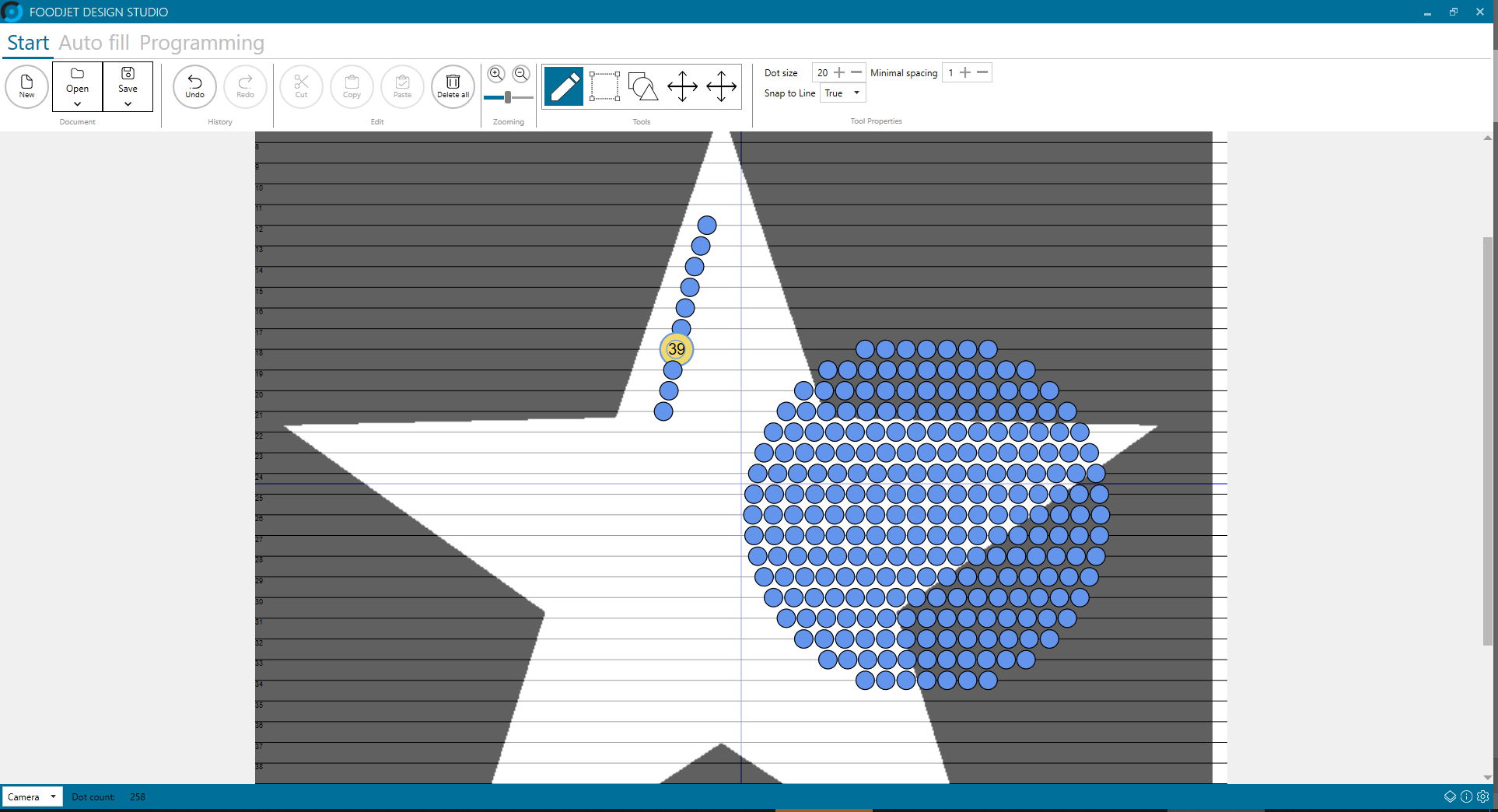
Typical applications that use vision technology
The depositing solutions of FoodJet are always tailor-made to suit the needs and wishes of your production process. This means that no machine is exactly the same! This allows us to manufacture depositing solutions for a wide range of depositing materials. Take a look at our similar applications:
Would like to receive our articles and updates?
Sign up for the FoodJet Newsletter.